Fuel Desulphurisation
Current Context and Challenges
We are currently suffering the effects of environmental pollution caused by the emission of pollutants such as carbon dioxide (CO2), CO, particulate matter (PM), Hydrocarbons (HC), nitrogen oxides (NOx) and sulfur oxides (SOx) to the atmosphere. The pollution can have both ashore and maritime origin but generally comes from the incomplete combustion of fuel, the thermal splitting of HC, the high temperature of combustion in the engines cylinder or the oxidation of sulfur (S) in the fuel composition.
Maritime transportation has an impact on the global climate and air quality as well, as a result of the CO2 emissions and other emissions that it generates, such as NOx, SOx, methane (CH4), PM and black carbon (BC). Until a few years ago, shipping remained the only sector of transportation not included in the Union’s Commitment to reduce Greenhouse Gas Emissions (GHG).
The Sulphur Emissions
Sulfur in any of its forms reacts with oxygen (spontaneously or upon burning), producing oxides (called SOx, of which sulfur dioxide (SO2) is the most known). These sulfur oxides, in the presence of humidity from the combustion processes, turn into acids, such as sulphuric acid (H2SO4) and hydrogen sulfide (H2S) that can originate environmental problems, like acid rain.
Acid rain is harmful to many sectors: agriculture, damaging soils; wildlife, causing deforestation and oceans acidity; damaging monuments; and being extremely harmful to human health, associated to respiratory and cardiovascular diseases, and even cancer.
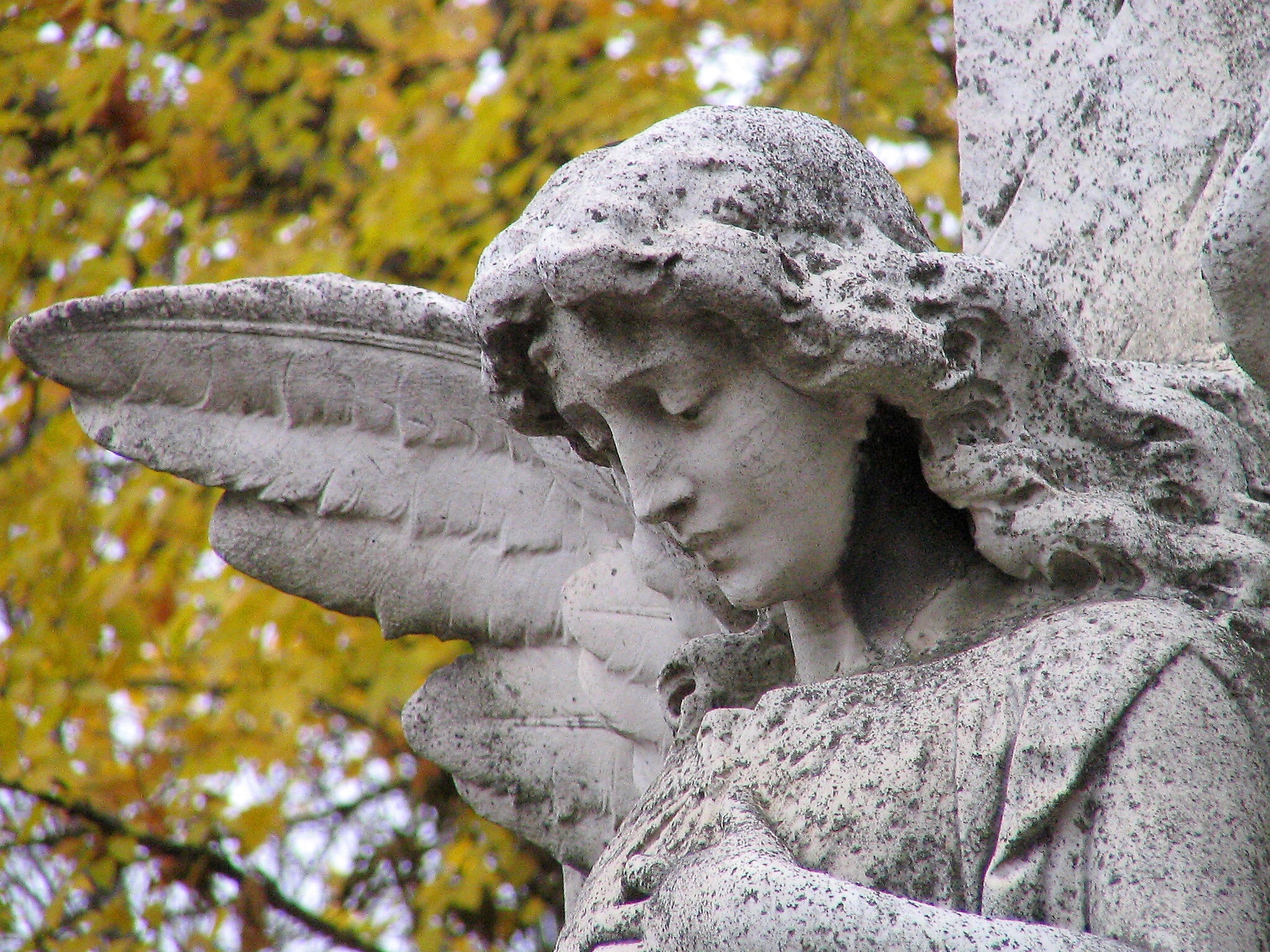
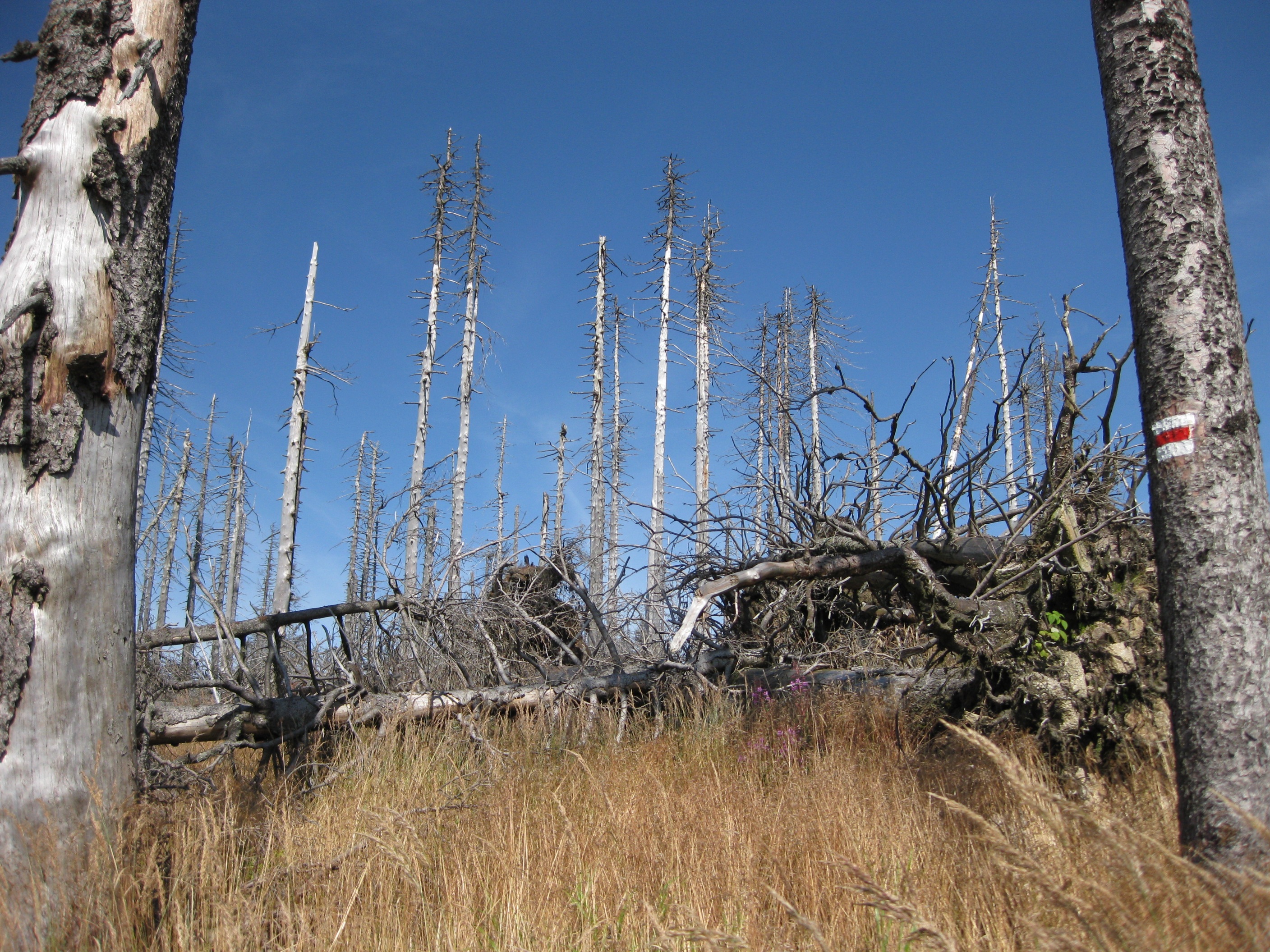
Sulfur is also responsible for the emission of particulates (soot) as the filters used in the means of transportation are rapidly degraded by fuels with a high sulfur content.
In this specific case, MARPOL stipulated limits on sulfur content in Marine Fuel Oil (HFO) as it can be seen in Figure 2. These limits are even more restricted in ECA areas:
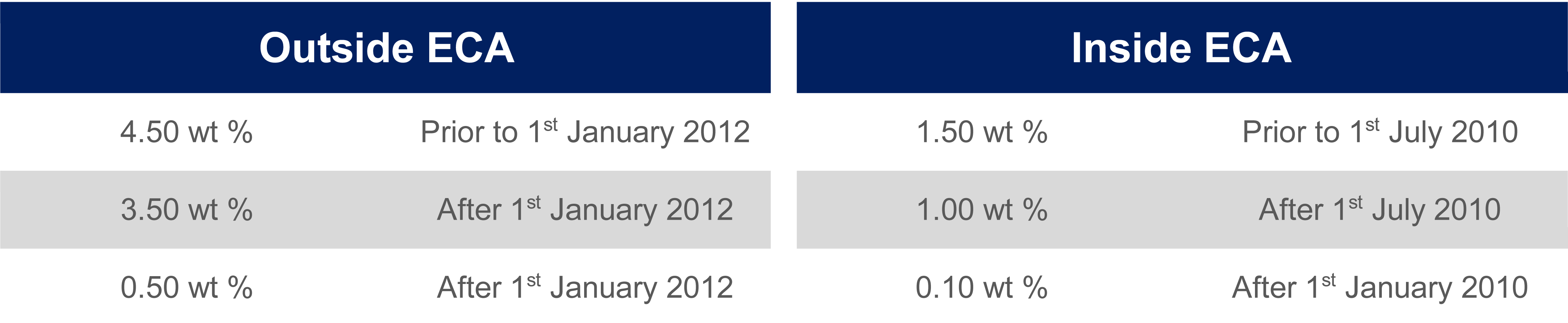
- Until 30 December 2011, MGO maximum content of 1.5% and MDO a maximum of 0.5%;
- From 1 Jan 2012, MDO with a maximum sulfur content 0.1%.
- From 1 July 2009, MGO maximum content of 1.5% and MDO a maximum of 0.5% may be used;
- From 1 Jan 2012, MGO or MDO with a maximum sulfur content 0.1% may be used.
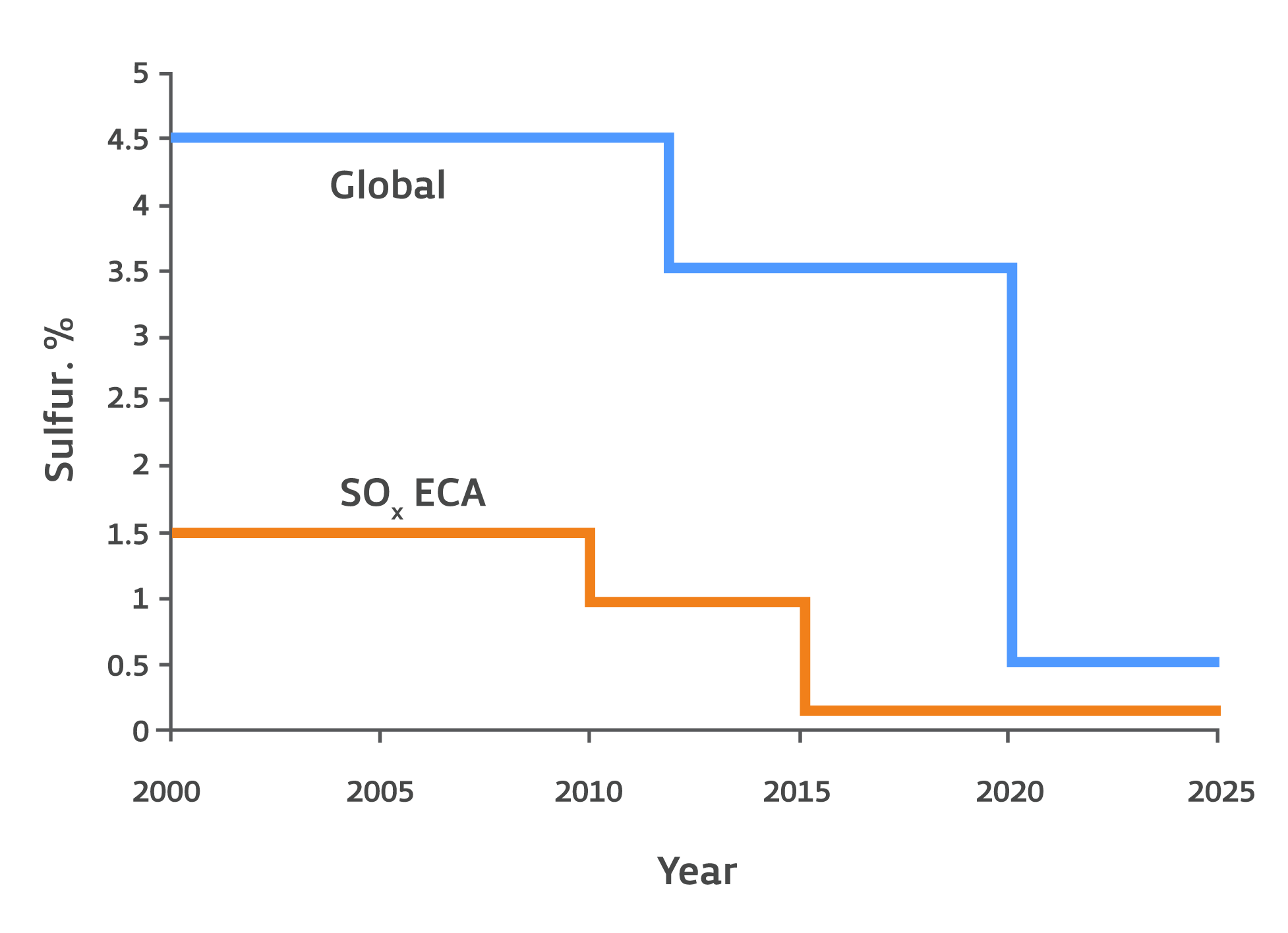
Different Techniques to use Low-Sulphur Fuel
There are several technologies that can be used in order to prevent the effects of SOX emissions: the use of low-sulfur fuel, the use of Flue Gas Desulphurization (FGD) techniques or desulphurization itself.
The first option has an economic impact related to their higher costs (low-sulfur heavy fuel has a somewhat higher price than the high-sulfur heavy fuel, due to increasing demand and the cost of the desulphurization process – Figure 3).
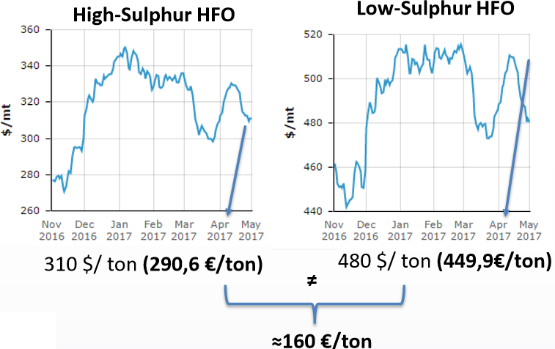
If it is considered, for example, a ship that processes 4 ton of HFO per hour, it corresponds to a consumption of 35040 tons/year of HFO. That corresponds to a significant investment representing 15,77 M€/year. Another important aspect is the fact that HFO with low-sulfur content has a limited availability. It is foreseen that only HFO with high sulfur levels would be available in a few years period. In that way, ship owners must pay for the fuel high emissions.
Also, there are operative problems considering low-sulfur alternatives to HFO, such as Low Sulphur Distillate Oils (LSDO), since ship owners and manufacturers of marine engines have limited experience using these types of fuel. Furthermore, modifications of the installations are necessary due to the requirement to use such fuels. Regarding operational safety and the ship itself, engines, pumps, boilers and boiler burners should be properly adjusted for the maintenance and burning of LSDO.
As mentioned above, another interesting technique that can be used to remove SOx is the Flue-Gas Desulphurization (FGD). It is a set of technologies used to remove sulfur oxides from exhaust flue gases of fossil-fuel power plants, and from the emissions of other sulfur oxide emitting processes. Though these technologies have several disadvantages:
- High operating costs;
- Increase in power consumption;
- Increase in dust emissions;
- Cannot be used for waste gas SO2 concentrations greater than 2000 ppm;
- Disposal of waste products with significant costs;
An ultimate alternative would be to resort on Desulphurization Techniques. Desulphurization has been commonly used, but many different techniques have been implemented industrially. Among them, the most classic is the Hydrodesulphurization (HDS). This classical process has been implemented in refineries and requires extreme operational conditions: high pressures (30 – 130 atm), high temperatures (300 – 400ºC) and require a considerable amount of thermal energy. Another risk is the use of hydrogen and the possibility of leakage through the reactor walls. The reaction takes place in a Fixed-Bed reactor, used an expensive solid or metallic catalyst, such as Co/Mo or Ni/Mo.
The Hydrodesulphurization (HDS) has some limitations to be pointed out, namely the fact that only enables the conversion of limited sulfur organic compounds present in fuel (Thiols, Thiophenes, Mercaptans, Thioethers, and Disulfides). Relatively to other sulfur compounds like Aromatic and cyclic (Benzothiophenes (BT) or dibenzothiophenes (DBT)) can hardly be removed by this technique.
Another aspect that limits the use of HDS is that it can only be applied for high production capacity factories – large refineries (requiring high reactors and high reaction times). After HDS other technique has been developed, the Oxidative Desulphurization (ODS). ODS is based on the use of a chemical with high oxidative potential: Hydroperoxide (in most cases H2O2-50% V/V), that will oxidize free and molecular sulfur to its oxide form (Sulphones and Sulphoxides), easier to remove from fuel (substantially more polar than sulfides).
The oxidant used although it is not a pollutant or harmful to the environment, instead it is expensive and potentially dangerous. This technique allows removing sulfur compounds resistant to HDS, due to the oxidation step. It allows to work with more reasonable operatory conditions (lower temperatures and pressures), don’t require as much thermal energy as HDS, being compatible with smaller processing units in terms of capacity. More recently some studies considered the advantage of combining the oxidant step with the effect promoted by Ultrasounds (Ultrasound – Assisted Oxidative Desulphurization -UAOD).
The fundamentals consist in combining the fuel with the oxidizing agent (hydroperoxide) in the presence of an aqueous fluid (for example water), being applied ultrasound to increase the reactivity of the species in the blend. As ODS it enables the users to operate at ambient temperature and atmospheric pressure, to selectively remove sulfur compounds from hydrocarbons. On the other hand, UAOD requires the use of a solid catalyst (Tungstate: CuSO4 or Fe (II)) to regulate the activity of the OH radical. It also requires a phase transfer agent (PTA) to accelerate the conversion of sulfides to sulfones. A final separation step of the technique involves a step of S/L extraction or L/L extraction to separate the sulfones from the fuel. UAOD permits to remove sulfur compounds from fuel with a yield of 99,90%.
The fundamentals of DESulphur – TecnoVeritas’ Disruptive Solution
TecnoVeritas has recently developed a Desulphurization technique that can overcome some of the limitations of classical processes consisting in an effective and cleaner way to remove sulfur compounds from sulfur. Desulphur is a patented, new and innovative Desulphurization Process that can be applied to installations (shore and sea) which requires the use of Fuel Oil, Heavy Fuel Oil (HFO), Marine Gas Oil or Marine Diesel Oil.
Due to the restrictive regulation on sulfur content imposed, the lack of fuel with low-sulfur in the market, and to the need of restricting SOX emissions caused by the oxidation of sulfur in fuel, it was urgent to find the solution. With Desulphur, users can reduce the sulfur content of their fuels to levels allowed by the regulations at the same time it remains its desirable characteristics (thermal, physical and chemical properties).
The process is based in some of the principles and advantages of UAOD but uses a compound with a higher oxidative potential, which is produced on-site and is cleaner (non-pollutant) than hydroperoxides. The produced oxidant promotes a more efficient oxidation of the sulfur compounds present in liquid fuels. The production of the oxidant species combined with the ultrasound system will convert more efficiently the sulfur compounds into oxides and peroxides (due to the increase of reactivity), which are easier to remove.
DESulphur is easy to install, requiring no modifications to installations, since it can be installed “In-Line”. It is also easily adapted to different production capacities and flow rates. It can be implemented on board ships, allowing them to burn fuel with the appropriate sulfur content. The few resultant by-products can be treated as oil waste with onboard systems and dispensed in the usual way.
The process requires the addition of only a few components to the fuel (cheap, easy to obtain and recoverable in the process), and operate at reasonable operation conditions (Low Temperatures and Atmospheric Pressure). The process takes into account the oxidation of sulfur species existing in fuel, to oxides and peroxides that are easier to remove. The oxidation process occurs efficiently due to the presence of an oxidant produced in situ and due to the effect of an ultrasound system that creates cavitation and promotes the thermo-ionic dissociation of the water presented in the fuel. A phase separation step allows removing the undesirable components from fuel, obtaining a treated fuel with low-sulfur content.
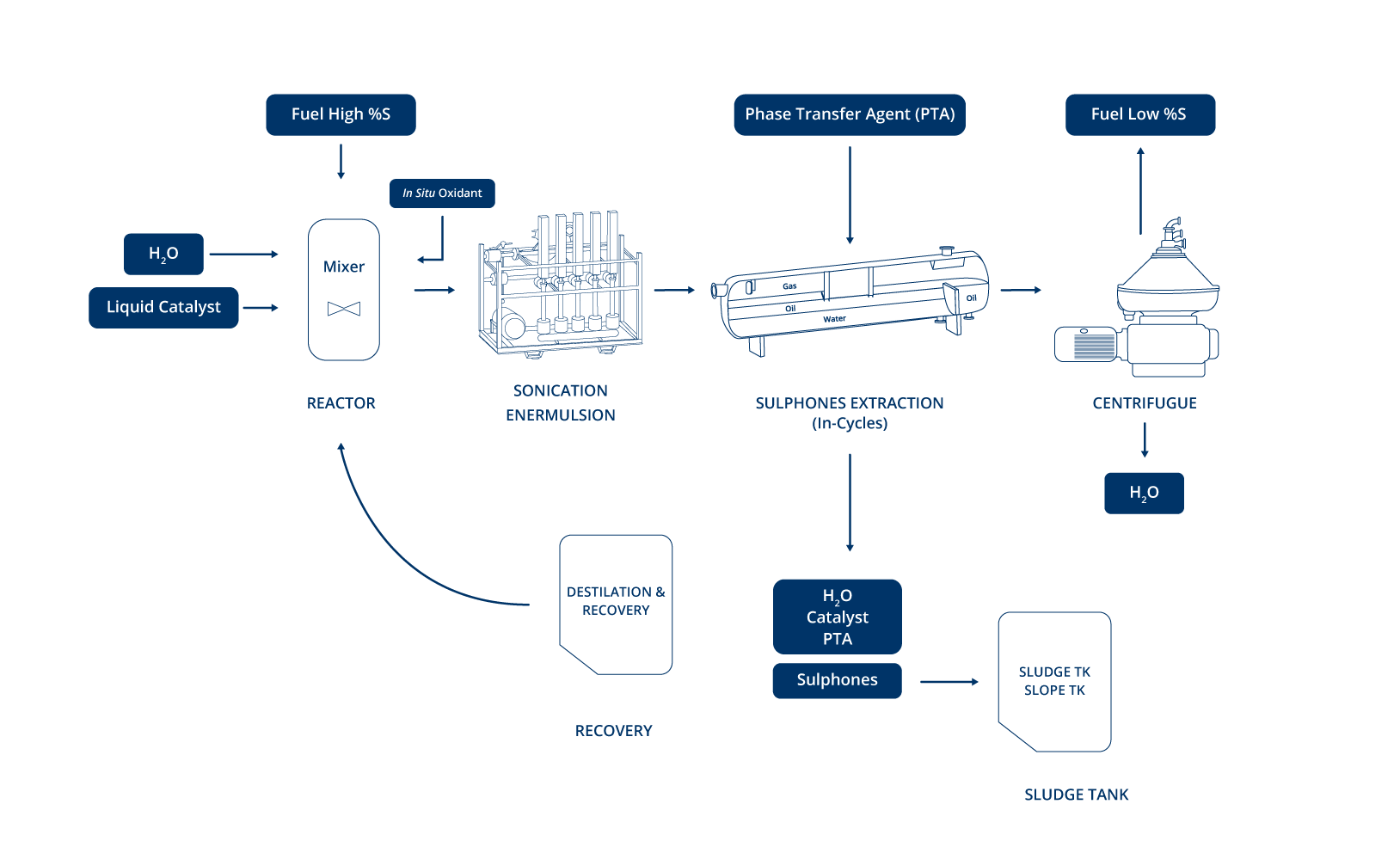
The Advantages
Economic
- The oxidant agent is produced in situ, therefore there is no need to add external compounds to the process;
- The process doesn’t require significant amounts of energy, presenting low operation/processing costs;
- All reagents used are not expensive and are relatively easy to obtain. These reagents can be recovered in the process with high yields;
- DESulphur uses relatively low temperatures and pressures (which involve lower costs), comparing to HDS, for example.
Security
- The process doesn’t present any safety hazard in terms of storage and handling, and all operative conditions are reasonable.
Environmental
- Process compatible with low flow rates, it can be implemented on board ships allowing them to burn fuel with the appropriate content of sulphur. By-products can be treated as oil residues by dedicated on-board systems and dispensed in the usual way.
The TecnoVeritas Desulphurisation technique is disruptive compared to the other classic techniques, due to the fact it uses a higher oxidative potential agent produced in-situ and cleaner. The produced oxidant guarantees in combination with the ultrasound effect a more efficient oxidation of the Sulphur species, allowing an easier removal.
The purified fuel (with lower sulfur content) maintains its desirable properties and can be used for maritime applications, but it is not limited to it.
Market and Applications
It can be used on a global scale (within maritime and industrial sectors), with a special interest in countries with seaports delivering greater economic, energy, operational/safety and environmental advantages. An example of sectors in which it could be used is petroleum industry, waste treatment and recovery of fuels, fuel producers, global industries that use heavy fuel in their activities or naval sector.
Conclusions
A brief economical evolution of the process was made to establish its viability. For instance, consider an installation that processes 4 tons of fuel per hour, the estimated investment is calculated to be recovered in about 9 months. The calculations were made taking into account the current fuel prices, assuming a unit utilization factor of 80%, and including the maintenance cost of the desulphurization plant.
TecnoVeritas developed a revolutionary product that could be the solution to solve a global problem of harmful emissions to the environment. It can offer numerous advantages compared to conventional desulphurization techniques. Its applications can be applied to a worldwide level, considering the diversity of customers that can go from industrial to the maritime sector.